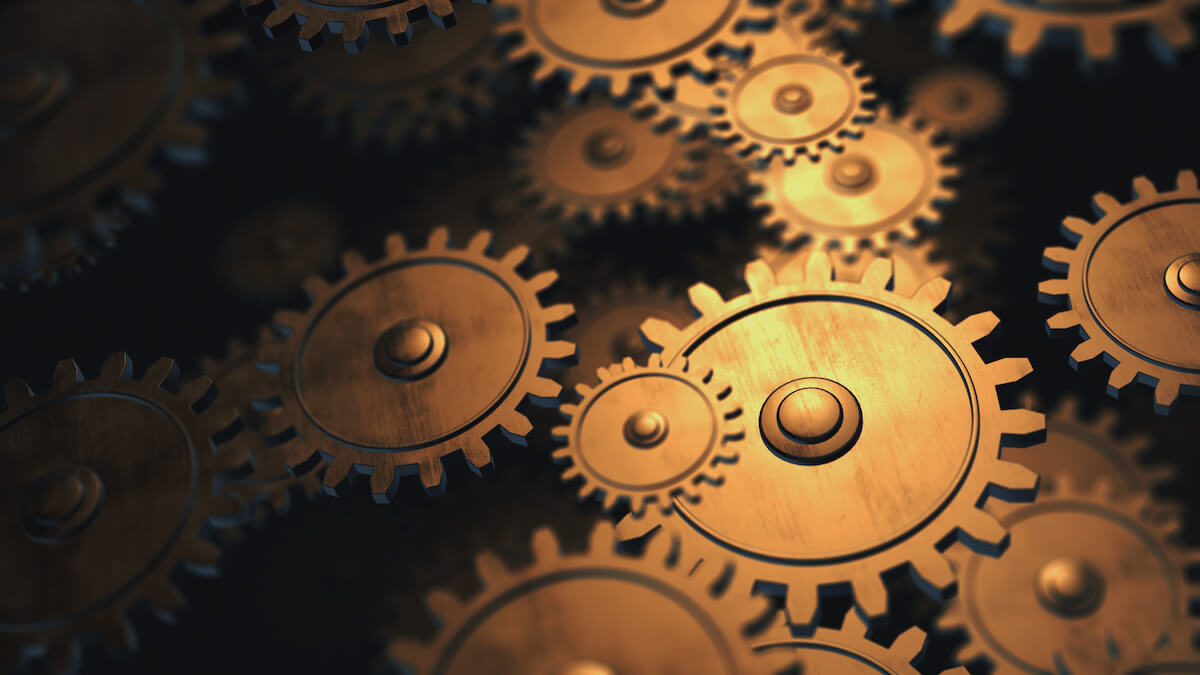
Easily Determine Required Tolerances Within PTC® Creo® CAD Software
Calculate Tolerances, Generate Reports, and Work Quickly Within Creo
Companies seeking to embrace mechanical variation management to improve their products face the pressure of quality assurance, supply chain variability, design complexity, time-to-market, and more. It’s crucial to make design activities, such as assigning accurate tolerances, as fast and easy as possible. With EZTA, your team can create, manage, and report on multiple 1D tolerance analyses while working on their product designs directly within Creo.
-
Define a stack-up in Creo in as few as five clicks.
-
Use, and link to, existing tolerance information, also called Product Manufacturing Information, or PMI, from the part files, ensuring that changes made within EZTA automatically update the source data.
-
Automatically generate the dimension sequence, or loop, between the endpoints of the gap being studied using Creo’s assembly constraints and part-level dimensioning scheme.
-
Easily evaluate worst-case, RSS, and generalized statistical analyses and understand which dimensions are contributing the most variation to each stack-up as well as all stack-ups combined.
-
Assess multiple stack-up analyses in different directions.
-
Integrate tolerance analysis directly within the 3D CAD model to support a MBD approach, promoting consistency, and providing comprehensive information for analysis and documentation.
-
Quickly change assembly assumptions between floating, biased, and centered when clearances are detected between parts, such as a bolt through a clearance hole.
-
List contributors to variation sorted from largest to smallest.
-
Draw conclusions about the overall design with a summary dashboard, showing the objectives and results of each stack-up analysis along with a visual indication of whether the requirement has been met.
-
Generate a detailed report quickly, including a graphical view of the dimension sequences for each of the stack-up captured with the included snapshot tool.
Improve Tolerance Analysis While Working on Designs
Our seamless in-CAD software makes tolerance stack-ups faster, more accurate, and easier than ever.
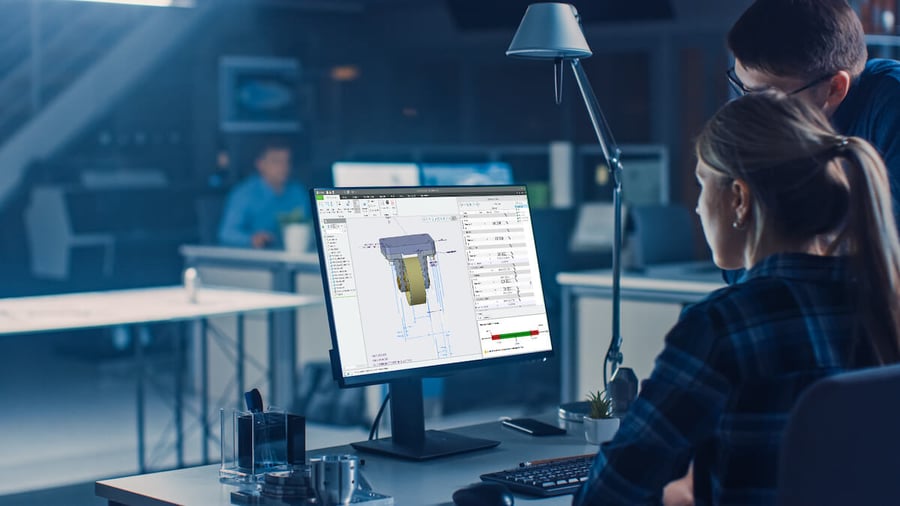
EZTA Offers Effortless Precision Inside PTC® Creo®
When design engineers are working on detailed drawings in Creo, they rely on EZTA to quickly determine appropriate tolerances to their part dimensions without transferring the data back and forth into spreadsheets. The embedded EZTA tool allows them to shift between creating features in the CAD models and assigning precise tolerances swiftly.
But that’s not all. Companies across varied industries rely on these benefits when they use EZTA.
-
Removes the necessity for manually configuring formulas and calculations, saving time and minimizing the risk of errors.
-
Improves consistency by automatically updating all tolerance values affected by a modification without the user having to manually adjust each individual analysis common when using spreadsheets.
-
Saves time and improves accuracy by referencing dimensions and their associated tolerances from within the Creo part models, eliminating the need for users to repeatedly input dimensions and tolerances when performing multiple stack-up analyses on the same design.
-
Offers additional features on top of 1D analyses, including a warning feature that alerts users to possible oversights in stack-up calculations.
Talk to a PTC® representative to implement EZTA in your organization and reap the benefits.
See PTC Creo EZ Tolerance Analysis in Action
Engineers can move faster with EZTA.
Our Full Suite of Software Products
Improve your products through mechanical variation management.
Comprehensive EZTA Training
Tolerance-Related Training
Discover More Tolerance Analysis Resources
Discover how to build and improve your enterprise with mechanical variation management resources.
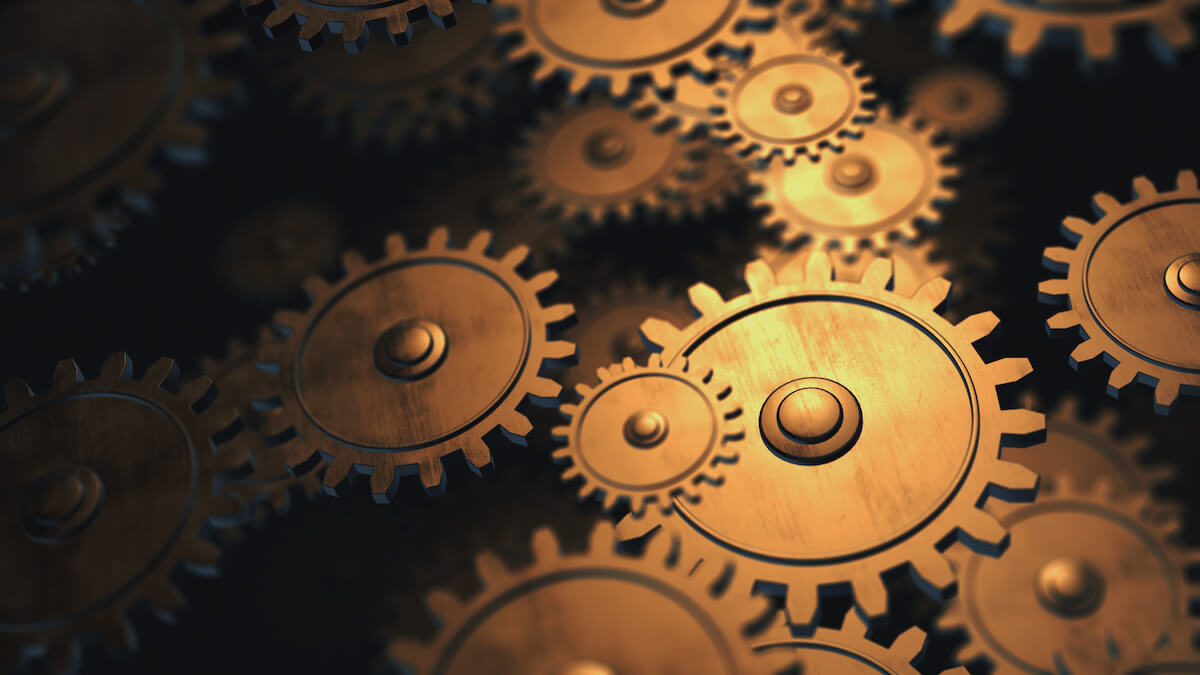
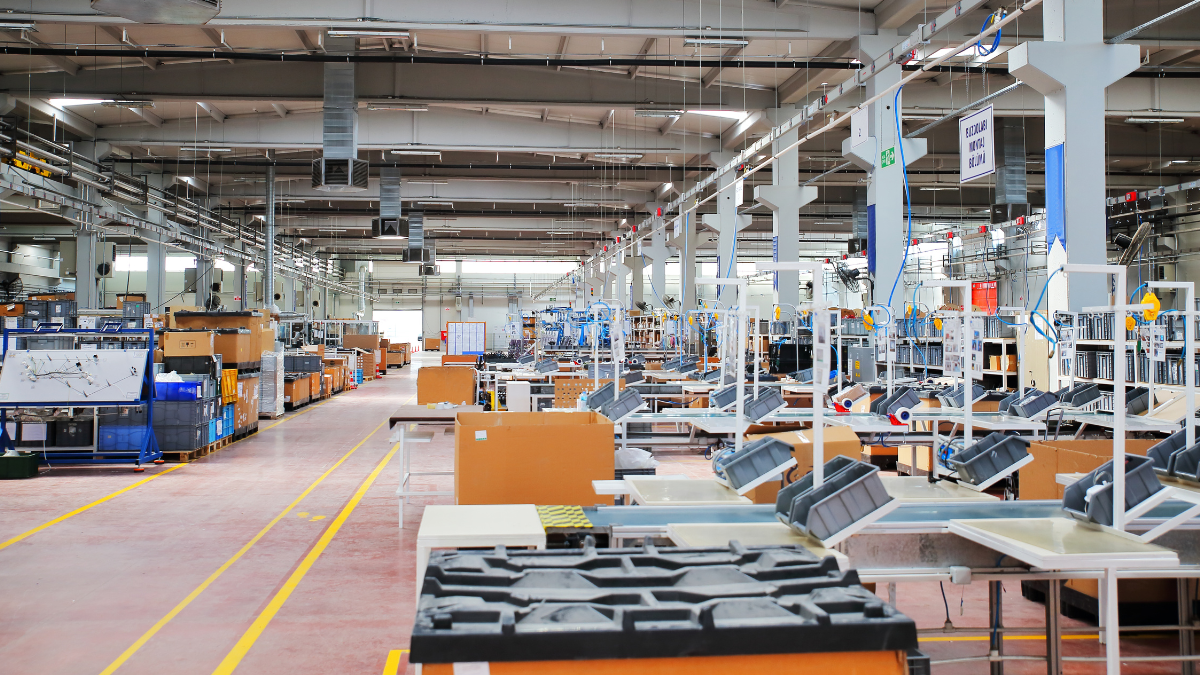
Common GD&T Errors and How to Avoid Them
